Berlin based MMDD MaxResolution3D GmbH is changing the way of manufacturing bike parts
- Divyank Sharma
- Sep 5, 2022
- 3 min read
Updated: Sep 19, 2022
Find out more about how 3D-printing can make your production cycle more sustainable.
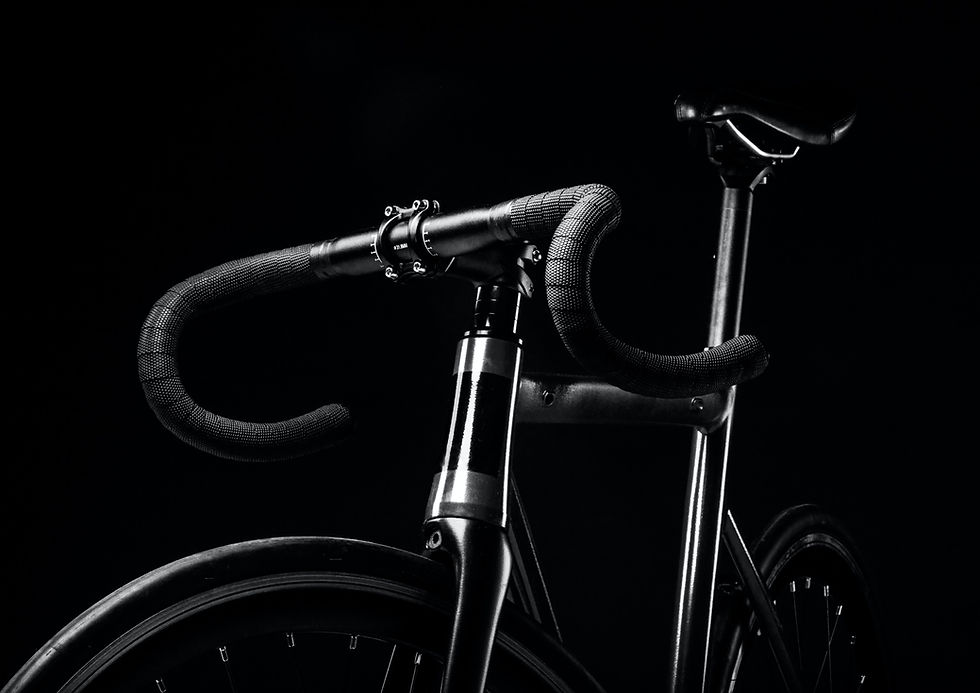
The European bicycle industry has annual sales of approximately 20 million bicycles. The industry consists of about 900 SMEs investing billions annually in R&D and giving employment to 120.000 workers. With a global market size of 58.15 billion euros in 2021 and an expected compound annual growth rate (CAGR) of 8.2% from 2022 to 2030, the bicycle market is one of the largest and fastest growing industries in the world. With the development of pedelec/e-bikes, the electric segment is the fastest growing within the industry. Around 17% of bicycles sold in the EU today are electric, while this percentage might reach 50% in some countries.
For a long time, bicycles have been people's preference as a convenient form of exercise to ensure a healthy life, free from obesity and other disorders. The increasing traffic congestion and less parking space are tempting people to opt for bicycles for short and middle distances. In our new world, with the challenges of growing pollution and global warming, people are now becoming more aware and responsible towards the environment by utilizing sustainable means of travelling as with bicycles, e-bikes and pedelecs. Both people and organizations are aiming to find new ways of mobility within a sustainable product chain of a lesser time window for a carbon-neutral world which gives it a huge range for growth in the future.
Although the bike business appears to be highly thriving, possibilities for growth and development have been harmed by the ongoing Russia-Ukraine conflict and the long-lasting Covid pandemic. Supply-chain disruptions, shortage of raw materials, delays in the production chain, etc., made everyone think about minimizing the goods' mobility to overcome future challenges.
With bicycle manufacturing having many parts to assemble at their junction point, they must reduce their supply chain nodes for better profits and fewer disruptions. Founder of SBlocs, a berlin-based cargo bike maker quoted, "Sometimes the process stalls while we remain to wait for particular components since we can't continue without them. Nevertheless, the entire production chain requires time, money, and patience. However, it is a common problem that all manufacturers deal with". 3D printing could be a great alternative here and local production on demand for low costs for the plastic parts could be the answer to all these problems by eliminating these interruptions and enhancing the value chain.
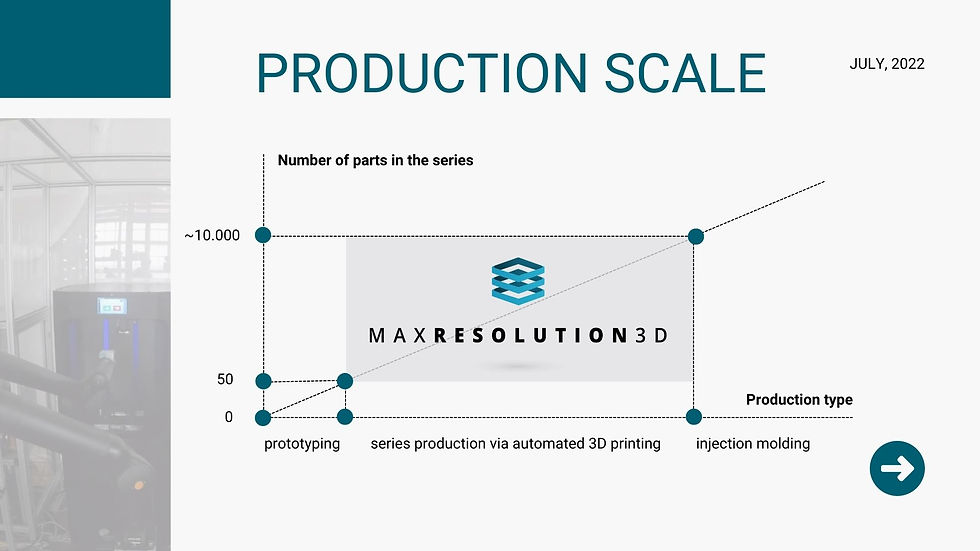
1.1 Our production scale showcasing the range of products we are capable to manufacture economically
The chances today are better than ever to switch production to series 3D printing. While just a little time ago, it was said that the parts manufactured via 3D printing do not meet the quality standards & requirements as UV-resistance, cannot be produced in large batches, or incorporated into the production chain, which led to the limited use of the technology. Now, automation is being integrated with 3D printers for on-demand automated series printing to ensure bulk production via 3D printing. Also, material science has made a huge effort in this field and materials are available that match the quality standards, allowing 3D printing techniques to manufacture a wide range of products.
A quick and sustainable method of producing your polymer components locally in Berlin is offered by MMDD MaxResolution3D GmbH. An automated 3D printing unit can manufacture 24/7 in huge batches per year while saving on mould costs and also preventing overproduction. With the flexibility of simple design adjustments, the technology also enables us to evaluate the part's functionality, quality, and design, allowing us to react with agility. With pedelec being on a boom, series 3D printing could be handy in complex part production.

1.2 Our bike part use case shows we can manufacture 1.630 parts per day
We have the bicycle market segment as our primary target by understanding that our technology and manufacturing process will eliminate the challenges faced and be economical and sustainable. We are productive, resulting in short waiting periods, and we can deliver your exceptional quality, industry-ready components throughout Europe in only a few days thanks to our fully automated production line.
Comentários